Having to give up and losing parts of one’s own body is an incisive point in the life of people treated with amputation and those who lose or lack limbs in any way. Whether it being the result of a disease, accident or a condition born with, amputees are confronted with life differently and must adapt to a world made for non handicapped people.
For people with amputated limbs, prostheses can provide a tool to master everyday-tasks, be more mobile and partake in society. Whilst many medical systems in high-developed countries provide modern prostheses and the connected care for their patients, low- to middle-income countries (LMIC) often face problems in accessing the same for their population.
For amputees, the missing limbs can cause social separation as well as disadvantages in work, which ultimately may result in poverty. Often, accommodation for accessibility and help to compensate disadvantages is hardly provided by governments of LMICs. The inability to support amputees adequately can deteriorate the quality of people´s life gravely.
A project of the Hasso-Plattner-Institute in cooperation with the global engineering program at Penn State University wanted at exploring the issue of prosthetic care and possible solutions to improve the situation for the people in LMIC using design thinking. They specialized on protheses for below-the-knee-amputees. As an international and interdisciplinary team, they aimed for a broad and open-minded approach to the topic. The university project evolved into a startup named Amparo and seated in Berlin.
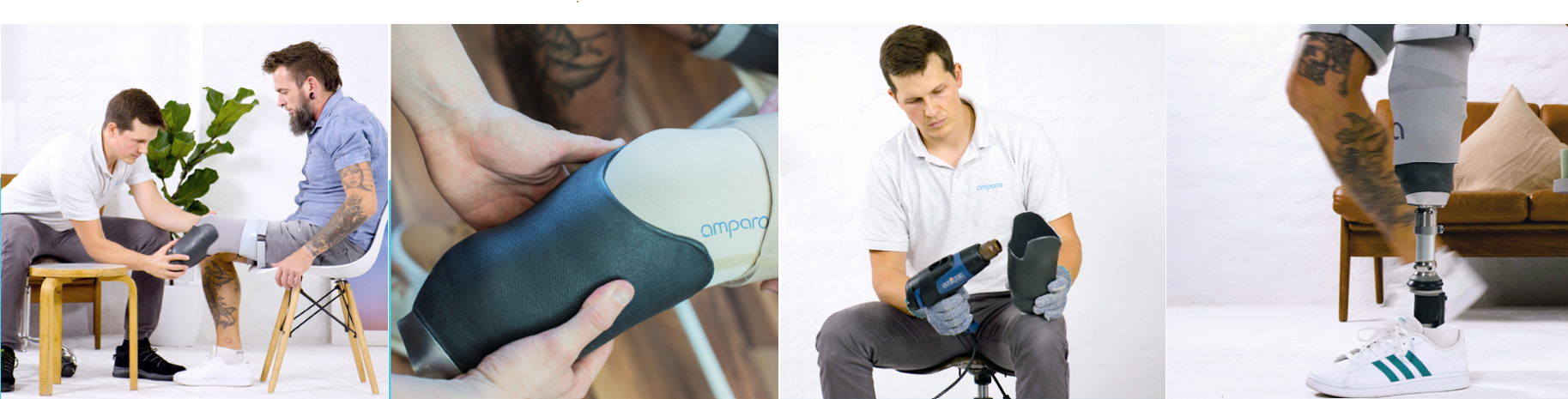
The process
The team started to assess the situation by gathering firsthand information. For this, conversation with amputees and orthopedic technicians was taken on, starting with German specialists but moving on to South Africa and eventually taking sources from around the world. Through this input the team could identify the socket of prostheses for below-the-knee-amputees as the key component for accommodating patients. With the socket, the residual limb is fixated into a bracket that allows the attachment of the artificial limb on a mount. The complications in providing a functional socket arise in the high individuality of it due to the fitting to the patient´s limb. This process is time-consuming and complex in procedure when using the industry standard for molding sockets, plaster-casting. Additionally, frequent replacements of the socket are necessary to accommodate for the changing limb particularly for patients with newly missing limbs. This situation results in requirement of frequent treatments, each with long durations to perform the fitting process and done by specialists.
The weak healthcare systems and few specialists in many LMIC however do not provide the required care which leaves only few people with demand of protheses to have access to them in a way that covers the needed support.
What the team derived from the problems in providing a socket for prostheses was that it would have to be more easily adjustable and usable to improve the situation. Besides reducing the problems in fitting they also aimed at more affordability and accessibility for patients in LMIC.
Searching for ideas to avoid the difficulties of the process, the team planned to remodel the fitting of the prosthesis. An alternative way to fit the socket to the limb is possible through choosing a material that can easily be formed and reformed.
At this point the university project ended after a duration of four months with many ideas gathered on how to proceed further on solving the problem. That is when the startup Amparo was founded by a part of the team. They were able to secure governmental funds and continue the process.
The team of Amparo researched and tested various materials before settling for Thermoplastic. It does not only allow for an improved adjustment to the patient through forming of the heated material but also for the repetition of the process as often as necessary. A socket from this material does not require special equipment to install and reduces the expenditure of time in comparison to plaster-casting.
Amparo developed prototypes using a user-oriented approach, that in the early stages mainly included feedback from experts. They also organized product trainings and service demonstrations not only for testing purposes but also to present their products to the stakeholders. Besides the customers those also included clinics since their approval of and interest in the product was necessary to make it available for users.
Although the team aimed at expanding the testing and prototype development to include feedback from the focus group in LMICs, their difficulties with winning over investors caused a change of concept. It led to a reorientation of the target market and accordingly of the targeted feedback group. With the center in Berlin and not in LMICs the possible investors assessed the risk of the geographical distance as to large. After the evaluation of the potential of the product in the German and European market, Amparo decided to focus their development locally first although still intending for LMICs long-term. With this reorientation, the product development now aimed for the application on newly amputated patients in Germany and Europe and their frequent demand of changes to the socket. Though accessibility was of lesser importance in this context, with the improved and easier fitting, request of the product successfully emerged and led to the growth of the startup.
Instead of outsourcing, Amparo decided for in-house production. This made easy and frequent alterations to the product possible that simplified the reaction to testing results. With distribution starting in Germany, the team was able to collect input about real-life appliance of their product and could implement improvements directly into manufacturing. This way their production became more cost-efficient compared to outsourcing it since a continuous development was intended.
During the production and testing phase, Amparo went through an improvement of the team´s organization as well. To help the team dynamics and workflow, a reconstruction appeared necessary. It was afterwards rated by the team as successful for the cause.
Results
Following the design thinking approach, Amparo ultimately developed their product “Confidence Socket”. The socket for attaching the prosthesis can be formed directly at the patient´s limb due to using thermoplastic. The molding is possible after heating the material and requires no heavy machinery or special tools, which makes it cost-efficient and simpler to use. Further less than two hours are needed to customize the product to reduce time-consumption. Multiple fittings anew are possible to accommodate the changing limb. With it, the company offers an alternative to model-casting that is highly shaped by the feedback of actual users and communication with stakeholders as well as ongoing development powered by the former.
Lessons Learned
Amparo illustrates how through design thinking and an interdisciplinary team revolutionary concepts can be developed and implemented. Besides this diversity, the dynamic of the team is equally important to realize the project.
With users in the focus of all developmental stages, the company ensured to develop a product that met the demands of customers, would allow them to enter the market successfully and spread wide.
Although the initial target group could not be accessed in the beginning, the contact with stakeholders led Amparo to establish their business close to home first which finally enabled them to reenter the original target countries. It only took a detour to achieve the destination, which was made possible to recognize and be successful with through communication.
Sources:
Amparo Prosthetics Ltd, https://amparo-prosthetics.com/about-us/
HPI School of Design Thinking (2017). Amparo – The Confidence Socket, https://hpi.de/school-of-design-thinking/in-der-praxis/amparo.html
AT2030 (2020). An AT Innovator case study: Amparo, https://at2030.org/an-at-innovator-case-study:-amparo/